Case Studies
Revolutionizing Automotive Domain: The Two-Wheeler Electric Vehicles Revolution – Powering Ahead with Cutting-Edge Mechanical Parts
DESIGN
Case Study 1: Improving Frame Body Quality for Electric Vehicles
Challenge: A leading manufacturer of electric vehicles faced a quality control issue with frame body components, leading to high rejection rates and scrap losses.
Solution: Adhithya Innovations conducted a thorough analysis and implemented process improvements, resulting in:
Key Outcomes:
- Significant cost savings
- Zero scrap value
- Zero-line stoppage
- Improved quality
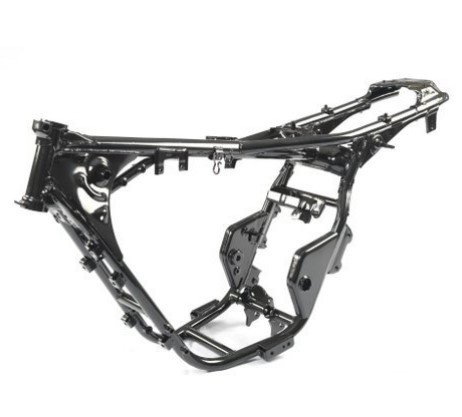
PRODUCT DEVELOPMENT
SUPPLIER SELECTION
SUPPLIER QUALIFICATION
Case Study 2: Reducing Battery Pack Rejection in Electric Vehicles
Background: A leading Electric Vehicle (EV) manufacturer aimed to improve the quality of their battery packs, Plastic Enclosures and reduce rejection rates.
Challenge: The company faced a battery pack rejection rate of 4%, resulting in significant costs and production delays.
Solution: Adhithya Innovations partnered with the company to implement a comprehensive quality control program, which included:
- Manufacturing Process Audits, Supplier Selection and Supplier Qualification
- Improved testing procedures
- Revised supplier quality standards
- Employee training and awareness programs
Results:
- Battery pack rejection rate reduced from 4% to 1%
- Significant cost savings
- Improved production efficiency
- Enhanced product quality and reliability

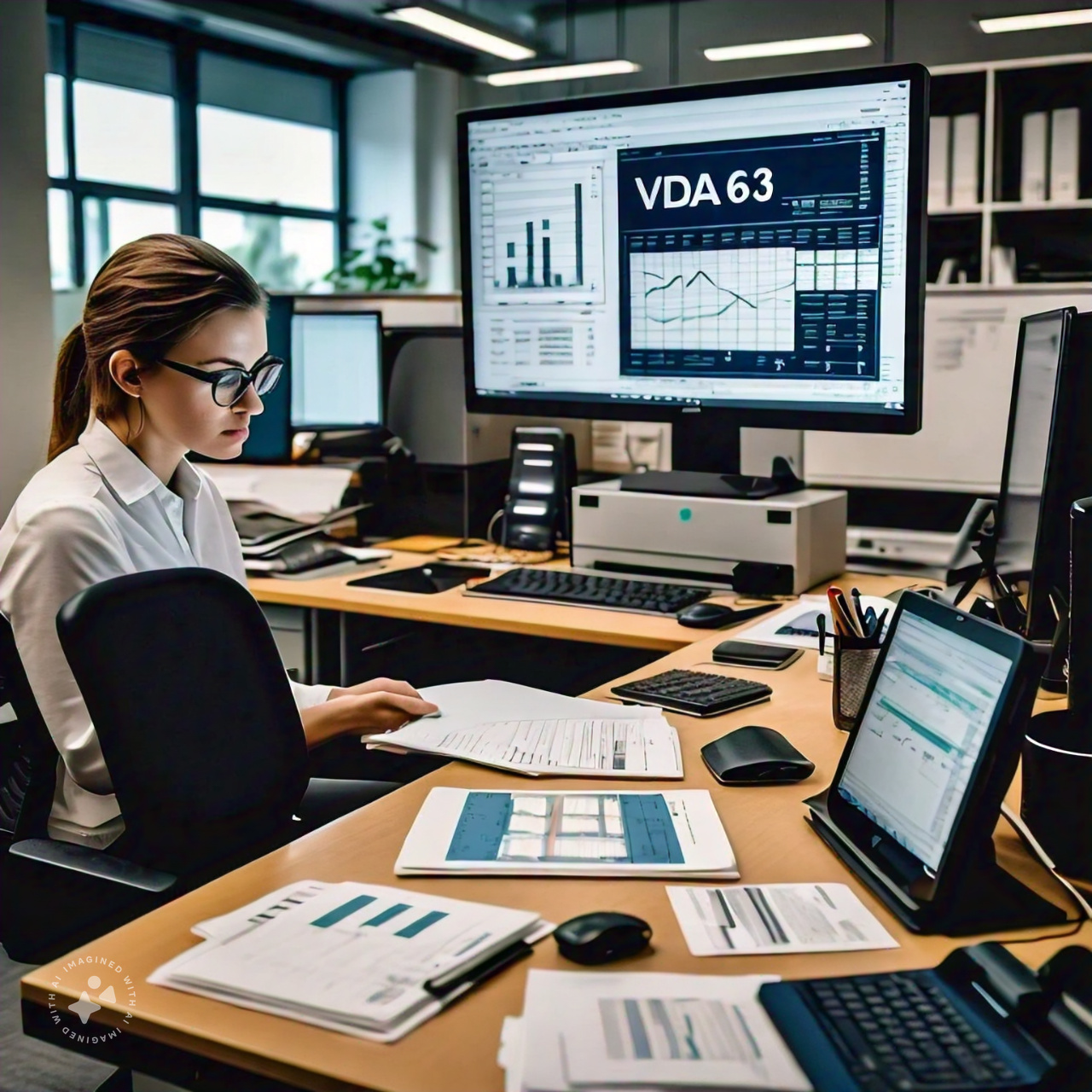
PRE-PRODUCTION VALIDATION
PRODUCTION PLANNING
INCOMING QUALITY CONTROL
Case Study 3: PPAP for Electric Vehicle Batteries
Background: Leading EV manufacturer needed a PPAP for battery packs to ensure quality and reliability.
Challenge: Implementing a comprehensive PPAP meeting international standards and customer requirements.
Solution: Adhithya Innovations collaborated to develop and implement a customized PPAP, including:
- Design and development reviews
- Prototype testing and validation
- Pre-production validation (PPV)
- Process capability studies
- Initial process capability approval
- Qualified laboratory and testing facilities
- Continuous monitoring and control
Results:
- Successful PPAP implementation for electric vehicle batteries
- Ensured compliance with international standards and customer requirements
- Improved quality and reliability of battery packs
- Enhanced customer satisfaction and trust
- Reduced production costs and improved efficiency
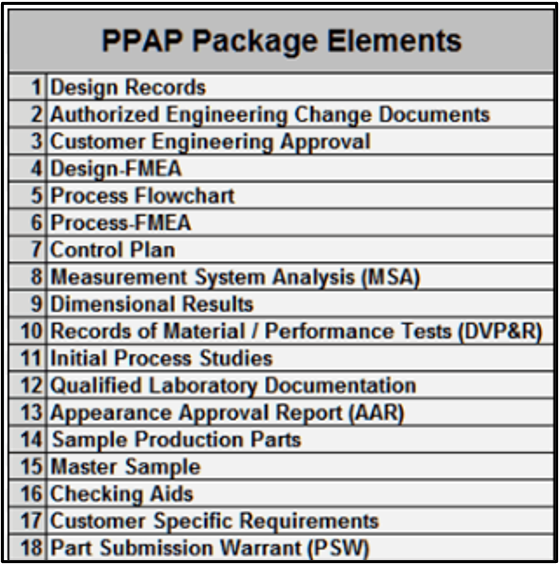
PRODUCTION AND ASSEMBLY
Case Study 4: Production & Assembly in EVs
Challenge: Inefficient production & assembly processes in electric vehicle manufacturing.
Solution: Adhithya Innovations analyzed & optimized workflows, implemented lean techniques, automated assembly lines, enhanced quality control & trained personnel.
Results:
- 30% reduced production time
- 25% lower labor costs
- 20% improved product quality
Best Practices: Continuously analyze & optimize processes, leverage automation & technology, enhance quality control & train personnel.

PACKAGING
SHIPPING
Case Study 5: Packing & Shipping in EVs
Challenge: Inefficient processes damaged EV components, caused delays, and increased costs.
Solution: Customized packing, automation, optimized routes, and real-time tracking.
Results:
- 40% less damage
- 25% faster delivery
- 15% lower costs
- Happier customers
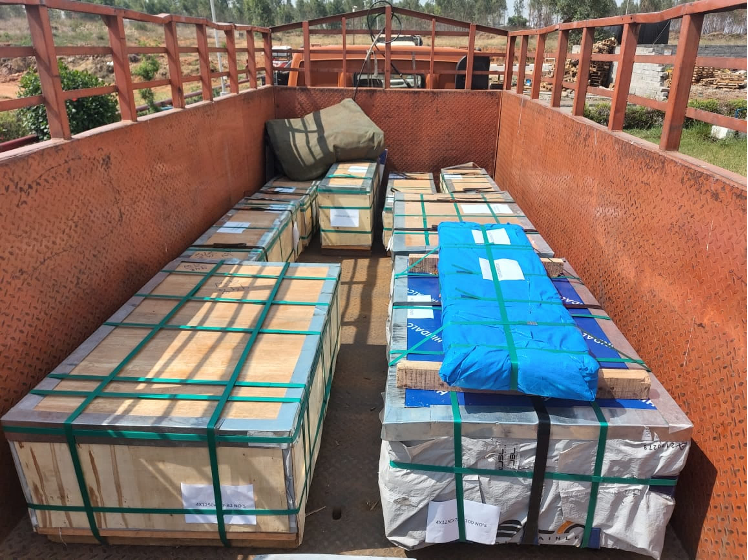
Transforming the Aerospace Industry: A Revolution in Customer Experience
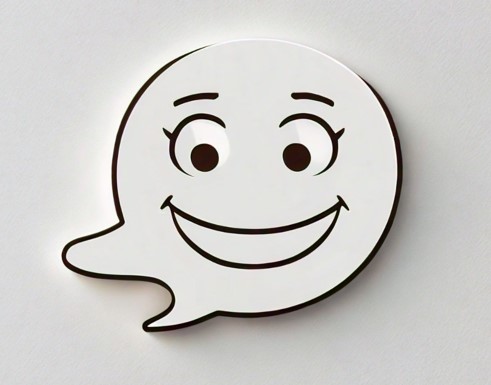
-
Incident Reporting: Easy submission of safety incident reports by aviation professionals
-
Data Management: Analysis of reported incidents
-
Data Analytics: Identification of trends, patterns, and insights to inform safety improvements
-
Stakeholder Engagement: Automated notifications and reports to relevant authorities, airlines, and other stakeholders
-
Enhanced Safety: Improved incident reporting and analysis, leading to proactive safety measures
-
Increased Efficiency: Streamlined reporting process, reducing manual errors and time
-
Data-Driven Insights: Actionable intelligence and industry stakeholders to inform safety decisions
-
Compliance: Adherence to international safety reporting standards and regulations
-
Increased reporting rates
-
Improved data quality
-
Enhanced safety awareness
-
Data driven decision making

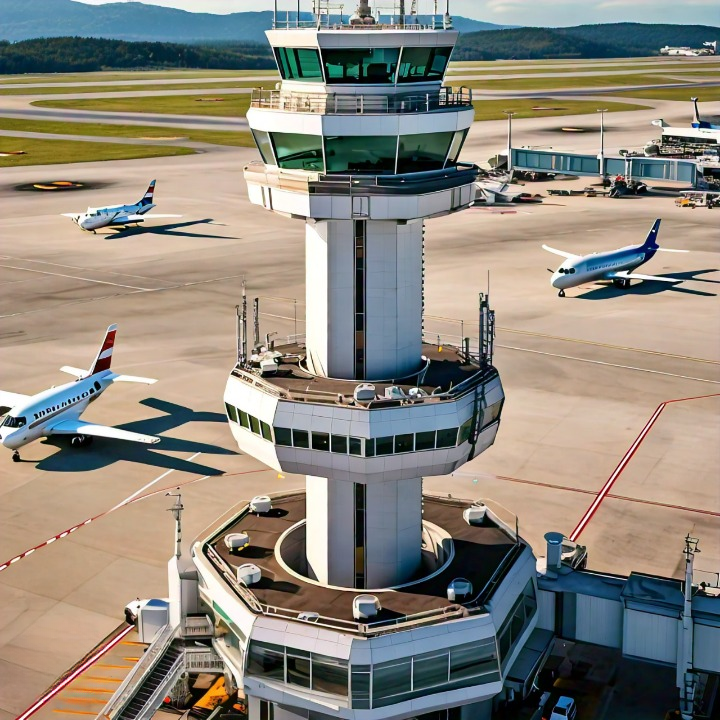
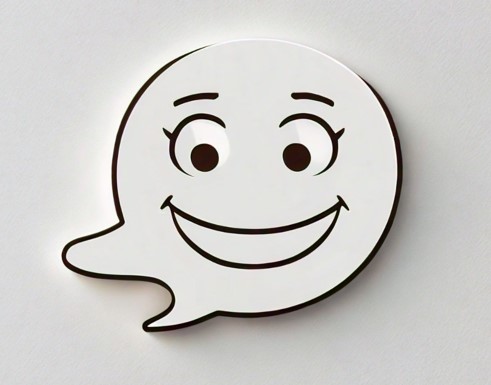
- Identify key variables contributing to flight delays from a large dataset.
- Our team applied Principal Component Analysis (PCA) to simplify the complex data set and determine the most significant factors causing flight delays.
- By pinpointing the crucial variables, our client can now implement targeted improvements to minimize delays and enhance overall flight operations.
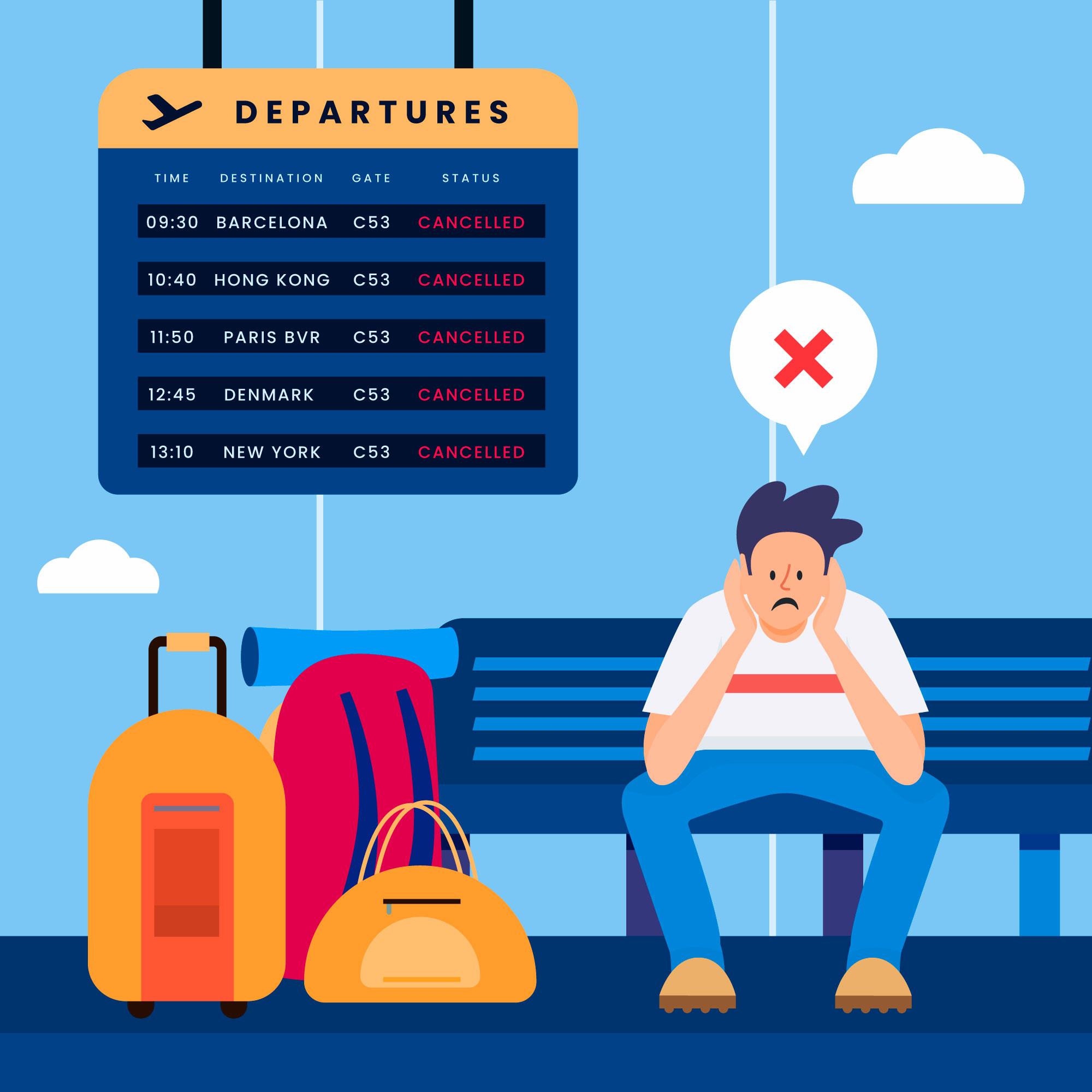
Focus on Bathroom Automation (Mechanical Design) – Adhithya Innovations As Catalyst For a Cleaner & Healthier World
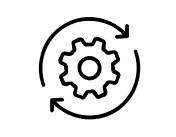
Case Study 1: Complete Concept to Production (Mechanical Design) – Bathroom Automation – Revolutionizing Commode Servicing (Automatic Flushing System)
Problem Statement
- Inefficient commode servicing processes, requiring complete removal and manual intervention, leading to increased downtime and maintenance costs.
Solution Overview
- Design and integration of a modular front enclosure, enabling swift access, repair, and replacement of internal components, minimizing labor requirements and enhancing overall hygiene.
Key Benefits
- Reduced Mean Time To Repair (MTTR)
- Improved First-Time Fix Rate (FTFR)
- Enhanced Customer Experience (CX)
- Increased Operational Efficiency (OE)
Implementation Roadmap
- Design For Manufacturability (DFM): Collaborative design and prototyping
- Verification and Validation (V&V): Rigorous testing and quality assurance
- Integration and Installation: Seamless deployment and commissioning
- Training and Support: Comprehensive maintenance and troubleshooting guidance
Conclusion
- Streamline bathroom automation servicing with a modular front enclosure, driving efficiency, productivity, and customer satisfaction.
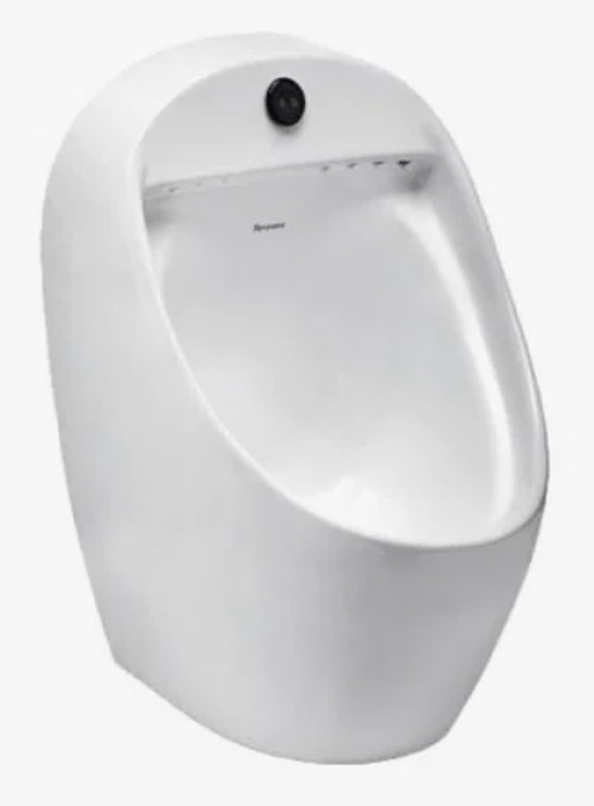
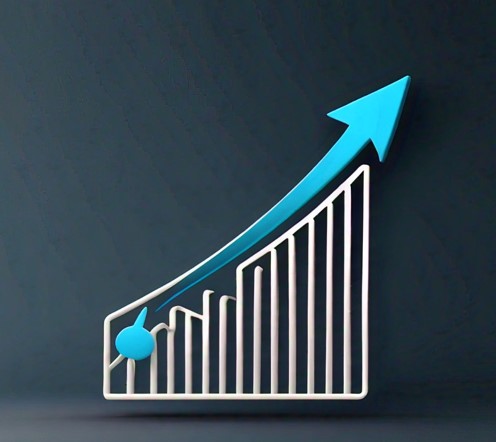
Case Study 2: Value Engineering in Electronic Flushing System
Challenge
- Complex design with many components
- High material costs due to excessive weight
Solution
- Simplified component architecture
- Minimized part weight through material optimization
Results
- 30% fewer components
- 25% weight reduction
- 20% cost savings
Methodology
- Functional analysis
- Design optimization
- Material selection
- DFMA implementation
Conclusion
- Value engineering optimized the electronic flushing system, reducing complexity, weight, and costs while maintaining performance.
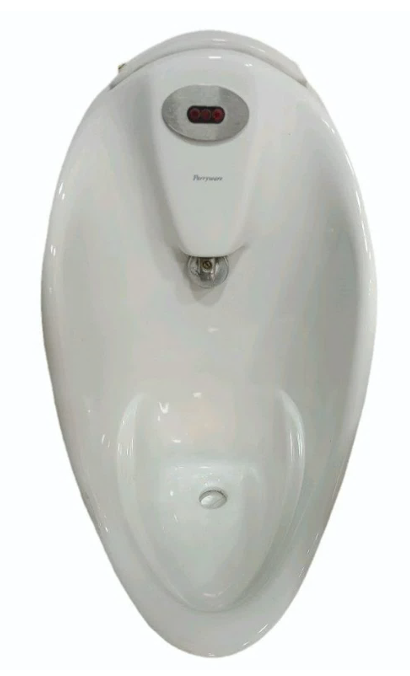